Rotogravure Hot Melt Lamination
HR Technologies has the capability to adhesively bond two layers of flexible rolled goods together using a Gravure style coating roller lamination process.
This is an extremely economical and ecofriendly bonding process with a large range of adhesive flexibility.
Our laminate composites will meet the most stringent OEM bond, flammability and environmental specifications.
No order is too small or large for our facility. Our machines are capable of processing small single roll orders up to the largest high volume continuous roll orders you may require!
Unlike flame lamination the hot melt lamination process maintains an open airflow bond layer. If air flow and acoustics are important, then HR Technologies Rotogravure lamination process may be exactly what you need.
The Rotogravure process is also used for coating rolled textiles or composites with a wide variety of available adhesives.
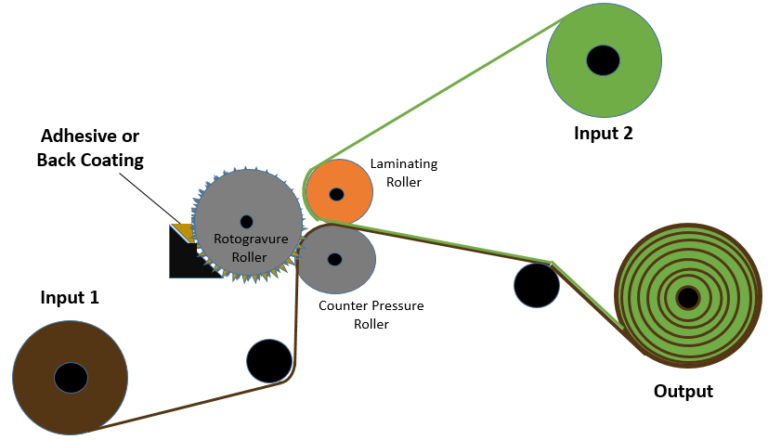
Rotogravure hot melt lamination offers numerous advantages for the automotive industry, specifically in the realm of automotive packaging and interior components. This technique involves laminating multiple layers of materials to create a robust and visually appealing structure. Let’s explore the key benefits of rotogravure lamination in the automotive industry:
Enhanced Protection:
Automotive components and parts often require protection from various environmental factors such as moisture, chemicals, and abrasion. Rotogravure hot melt lamination enables the creation of multi-layered structures with excellent barrier properties. By combining materials with different characteristics, such as films, foils, and adhesives, rotogravure lamination provides superior protection, ensuring the longevity and functionality of automotive parts during storage, transportation, and use.
Improved Aesthetic Appeal:
The automotive industry places a strong emphasis on design and aesthetics. Rotogravure hot melt lamination allows for the incorporation of visually appealing graphics, patterns, and branding elements onto various automotive components. The high-quality print achieved through this process ensures sharp, vibrant, and detailed images, enhancing the overall visual appeal of interior panels, trimmings, and packaging. This contributes to a more appealing and luxurious automotive experience for consumers.
Durability and Longevity:
Automotive components are subjected to rigorous use, including exposure to UV radiation, temperature fluctuations, and mechanical stress. Rotogravure hot melt lamination creates laminated structures that offer enhanced strength, durability, and resistance to wear and tear. The combination of different materials in the lamination process improves the overall strength and longevity of the components, ensuring they can withstand the demanding conditions of automotive applications.
Noise and Vibration Damping:
Automotive interiors often require materials that can reduce noise and vibration for a comfortable driving experience. Rotogravure hot melt lamination allows for the integration of sound-damping and vibration-absorbing materials into automotive components such as door panels, floor mats, and dashboard trim. This helps minimize road noise and vibrations, resulting in a quieter and more comfortable cabin environment for drivers and passengers.
Ease of Cleaning and Maintenance:
Automotive interiors often require regular cleaning and maintenance to maintain their appearance. Rotogravure hot melt lamination creates laminated surfaces that are easy to clean and resistant to stains, ensuring that automotive components can be maintained in a pristine condition. This benefit is particularly valuable for areas such as seat covers, door panels, and floor mats that are prone to dirt, spills, and wear.
In summary, rotogravure hot melt lamination offers several advantages in the automotive industry, including enhanced protection, improved aesthetics, durability, noise and vibration damping, and ease of cleaning. By leveraging the capabilities of this lamination technique, automotive manufacturers can produce visually appealing, durable, and functional components and packaging that enhance the overall driving experience for consumers.
Process parameters:
- Speed
- Pressure
- Pattern coating
–10gsm to 100gsm adhesive weight - Fullcover coating
–10gsm to 100gsm adhesive weight
Typical Process Inputs:
- Facing Materials (Input 1)
–PVC/PUR synthetic leather
–automotive interiors body cloth
–carpet
–non-woovens
–other “A surface” rolled goods - Backing Materials (Input 2)
–Open cell foams
–Closed cell foams
–Polyether/Polyester PU reticulated foams
–PET fiber
–PET Pointbond/spunbond
–other rolled materials - Hotmelt Adhesives
- Reactive Urethane Adhesive (PUR)
- Ethylene Vinyl Acetate Adhesive(EVA)
- PSA (Pressure sensitive adhesive)
–Rubber and Acrylic (PSA)
Available Products:
Custom weights, widths, and constructions are available
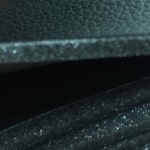
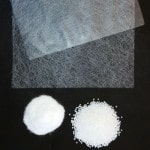
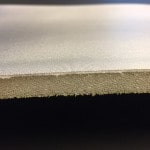
Our coated products have the potential to eliminate costly and messy spray adhesives from our customers’ facilities.
Call us to discuss how we can help you save money and improve plant working conditions.